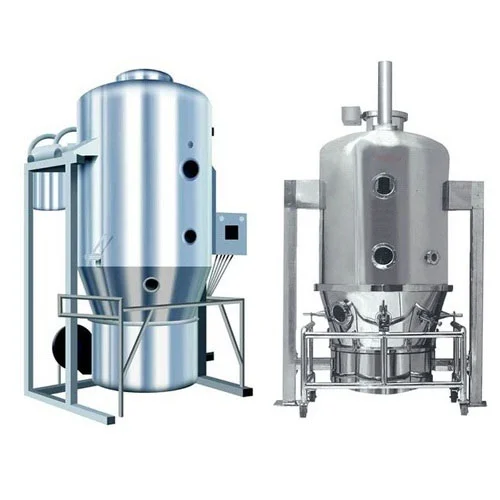
Fluid bed dryers (FBDs) have become an essential piece of equipment in various industries, including pharmaceuticals, food processing, chemicals, and more. They are used to dry granular materials by suspending them in an upward stream of air or gas, which enhances heat transfer and moisture removal. However, like any industrial machinery, to optimize the drying process and achieve the best results, certain operational best practices must be followed. This article will discuss the core principles of fluid bed dryer operation and the best practices that can help maximize efficiency.
Understanding Fluid Bed Dryer Technology
A fluid bed dryer consists of a drying chamber where air is passed through a perforated bed of material. This causes the particles to behave like a fluid, creating an efficient drying environment. The fluidization of materials allows for improved heat and mass transfer, leading to faster drying times and more uniform results.
The efficiency of a fluid bed dryer depends on several factors, including airflow velocity, temperature, humidity levels, and the design of the dryer itself. Achieving optimal performance involves maintaining balance across these variables to ensure that the material is neither under-dried nor overheated.
Key Factors Affecting Fluid Bed Dryer Efficiency
1. Airflow and Distribution
The airflow is one of the most critical factors in the efficient operation of a Fluid bed dryer. Air must be evenly distributed across the drying bed to ensure consistent fluidization. If the airflow is too high, it can lead to material loss, while insufficient airflow will result in poor drying.
Best Practice: Ensure the fan speed is adjusted appropriately to maintain consistent airflow throughout the bed. It’s also important to regularly check and clean the air distribution plates to avoid clogging, which could impair airflow and reduce drying efficiency.
2. Temperature Control
Temperature plays a vital role in the drying process, affecting the evaporation rate of moisture from the material. However, excessive heat can cause overheating and degrade the product quality, while insufficient heat will lengthen drying time, reducing throughput.
Best Practice: Maintain the inlet and exhaust temperature at an optimal level for the specific material being dried. Regularly calibrate temperature sensors and ensure that there are no temperature fluctuations within the drying chamber. This can help to achieve the desired moisture content in the shortest time.
3. Particle Size and Consistency
The size and consistency of the particles being dried directly impact the fluidization process. Large or irregularly shaped particles may not fluidize as efficiently, resulting in uneven drying.
Best Practice: Ensure that the material is pre-screened for uniformity in size before loading it into the dryer. If necessary, use pre-treatment steps such as sieving or milling to achieve a more consistent particle size, thereby improving drying efficiency.
4. Moisture Content and Material Characteristics
The moisture content of the material at the start of the drying process and its moisture holding capacity will influence how efficiently the drying operation occurs. Materials with high moisture content may require longer drying times, while materials with low moisture content will reach optimal dryness faster.
Best Practice: Regularly monitor the moisture content of the material throughout the drying cycle to ensure that drying conditions are adjusted as needed. Utilizing moisture sensors and feedback systems can help in real-time monitoring, allowing for automatic adjustments to drying parameters.
5. Exhaust System Management
The exhaust system is responsible for removing the moisture-laden air from the drying chamber. An effective exhaust system helps to maintain the air quality inside the dryer and ensures the proper removal of moisture, preventing its reabsorption into the material.
Best Practice: Ensure the exhaust system is capable of removing sufficient air and moisture without causing excessive energy consumption. Additionally, regular maintenance of exhaust fans and air ducts should be performed to avoid blockages that could reduce drying efficiency.
Middle Section: Importance of Equipment Maintenance
An often overlooked but critical aspect of maximizing the efficiency of a fluid bed dryer is maintenance. Over time, components like fans, filters, and air distribution systems can degrade or accumulate dirt and debris, impairing the dryer’s overall performance.
Best Practice: Establish a comprehensive preventive maintenance program that includes regular checks and cleaning of the dryer’s key components, such as the air filters, nozzles, and fluidizing plates. The fan impellers should be inspected for wear and tear, as even slight damage can significantly affect airflow and energy consumption.
Additionally, all mechanical parts should be lubricated as recommended by the manufacturer, and any signs of corrosion should be addressed promptly. By conducting these maintenance tasks regularly, you can ensure the dryer operates at peak efficiency, preventing unnecessary downtime and extending the life of the equipment.
Control and Automation for Precision
Incorporating advanced control systems and automation into the fluid bed dryer operation can significantly enhance efficiency. Automated control systems allow for real-time monitoring and adjustments of key parameters like temperature, airflow, and humidity.
Best Practice: Invest in an automated control system that can dynamically adjust the drying parameters based on the material’s moisture content or feedback from sensors. By automating the process, you can eliminate human error, achieve greater precision in maintaining optimal drying conditions, and increase overall throughput.
Efficient Loading and Unloading
The loading and unloading processes can also impact the efficiency of fluid bed dryer operation. Inefficient loading can disrupt airflow and lead to uneven drying, while improper unloading can result in material loss or contamination.
Best Practice: Load the material evenly across the drying bed to ensure consistent fluidization. Use appropriate loading techniques to avoid overloading or underloading the dryer. Likewise, ensure that unloading is done carefully to prevent contamination and product loss.
Conclusion
Fluid bed dryer technology is an effective method for drying materials in various industries, but its efficiency is largely dependent on how well the system is managed. By optimizing key factors such as airflow, temperature control, material size, and moisture content, and by ensuring the dryer is regularly maintained and automated where possible, significant improvements in efficiency can be achieved.
With the best practices outlined here, operators can ensure that their fluid bed dryer delivers high-quality results while minimizing energy consumption and reducing downtime. Whether used in pharmaceuticals, food processing, or chemicals, a well-operated fluid bed dryer will help companies maximize productivity and product quality.